To ensure high product quality and keep improving, we have built up a professional testing lab to conduct various types of testing with the components and LED fixtures.
From new materials to samples of new models, our dedicated testing team is responsible for comprehensive testings to output actual and precise data, which is essential to product development and improvement at TOPLUMIN.
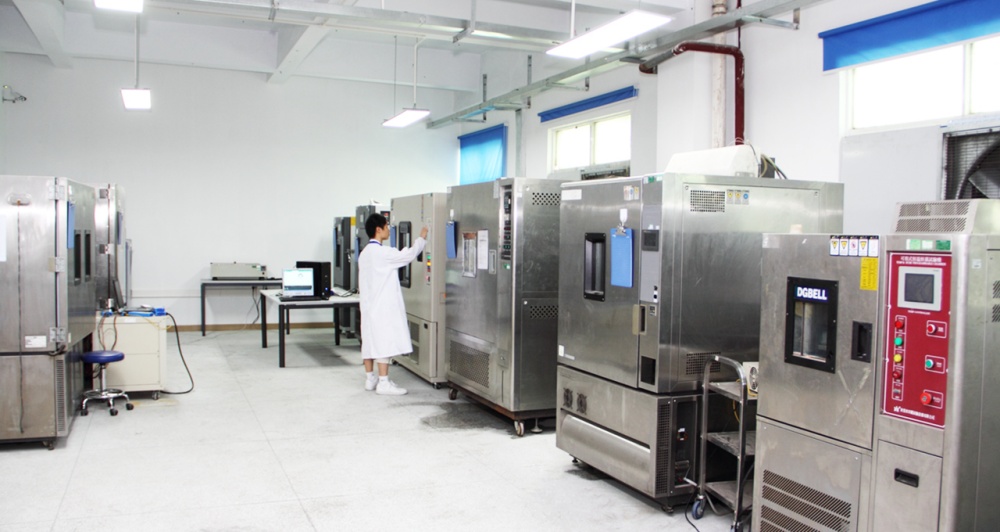
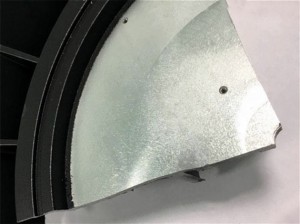
Cut Off Inspection
Cut off the lamp heat sink to inspect if there's any internal injury or sand and gravel mixed, which will weaken the heat dissipation of the LED luminaire to shorten its lifespan.
Aluminum alloy codes and processing technology: ADC12 - die-cast, 6063 - extruded, 1070 - cold forging.
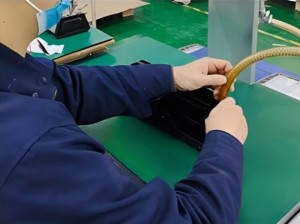
Gas-tight Testing
Any gas passing through the leak hole will produce eddy currents, and there will be part of the ultrasonic wave band, sound with frequency above 20KH that the human ear cannot relate to.
The digital ultrasonic leakage detection system uses sound to detect the air tightness of the lamp housing, thereby ensuring the waterproofing ability and IP rating of our LED luminaire.
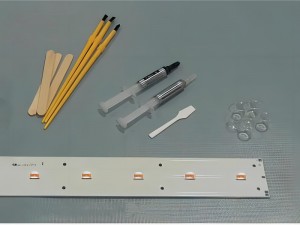
Chemical Compatibility of LEDs
The so called glass cap test operates high power LEDs together with material samples under accelerated lifetime conditions in a sealed environment.
Thus it can predict long-term interactions of materials like glues, sealing, pottings, etc. with LED performance.
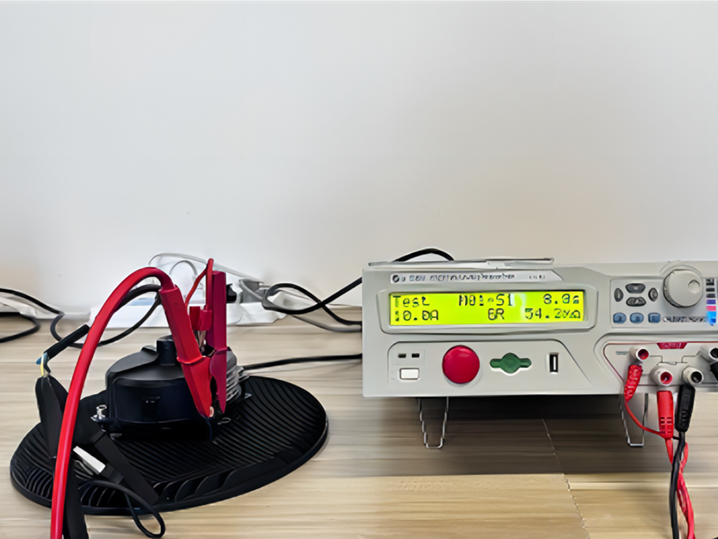
Hi-pot Test
Apply 3500Vac between the driver’s input and case of the LED fixture for 60s, making sure the measured leakage current meets the setting standard(≤5mA) without any spark or arc.
Hi-post testing is to ensure our LED fixtures are electrically safe for installers and end-users.
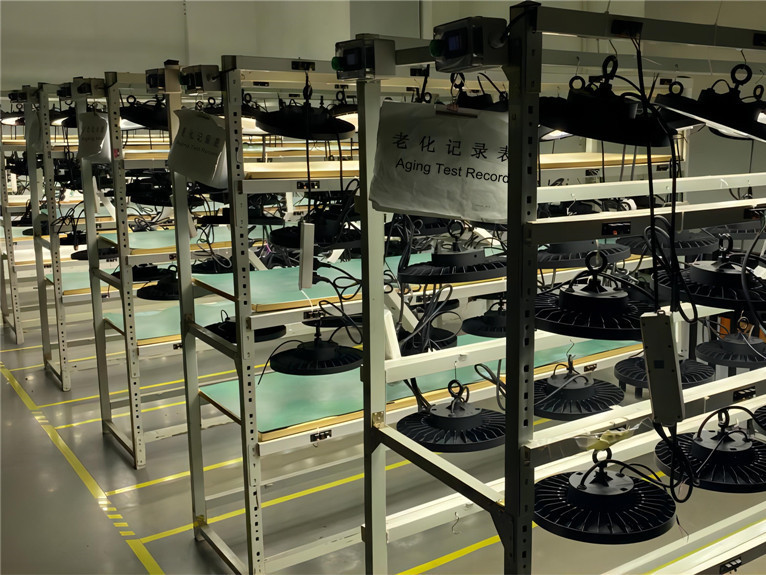
Aging Test
Every piece of the LED luminaire will go through 12h aging test after going off Toplumin's production lines, making sure that they're electrically stable before being packed.
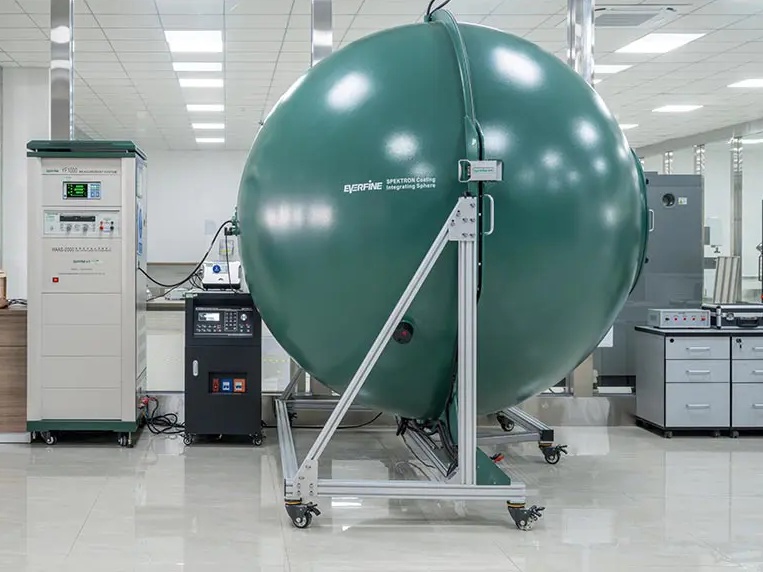
Integrating Sphere
Samples from every production batch will be tested to generate the test report including key light parameters(CCT, CRI, power and luminous efficacy, etc.).
Relevant test reports will be sent to customers along with other shipping documents before dispatch.
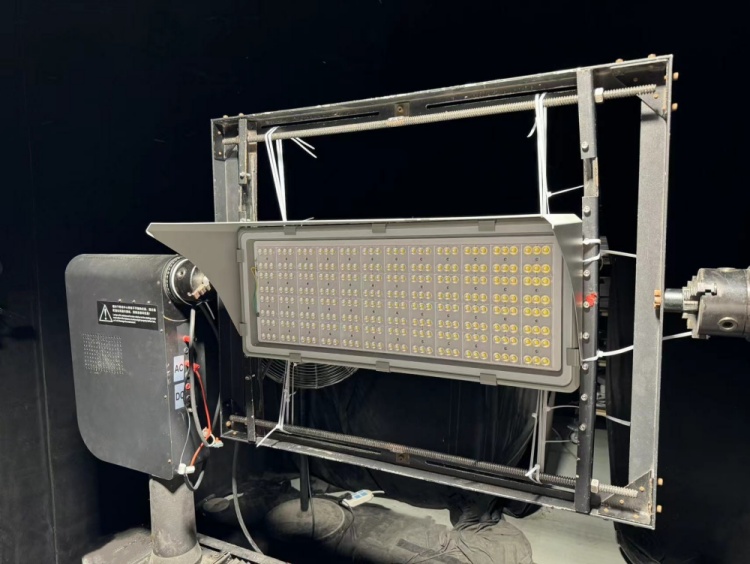
Goniophotometer
Test the luminous intensity and light distribution of the LED fixture to generate IES and LDT files, which are used in lighting design software(Dialux, Relux) for lighting planning and luminaires layout.
Test reports and files will be provided to customers upon request.
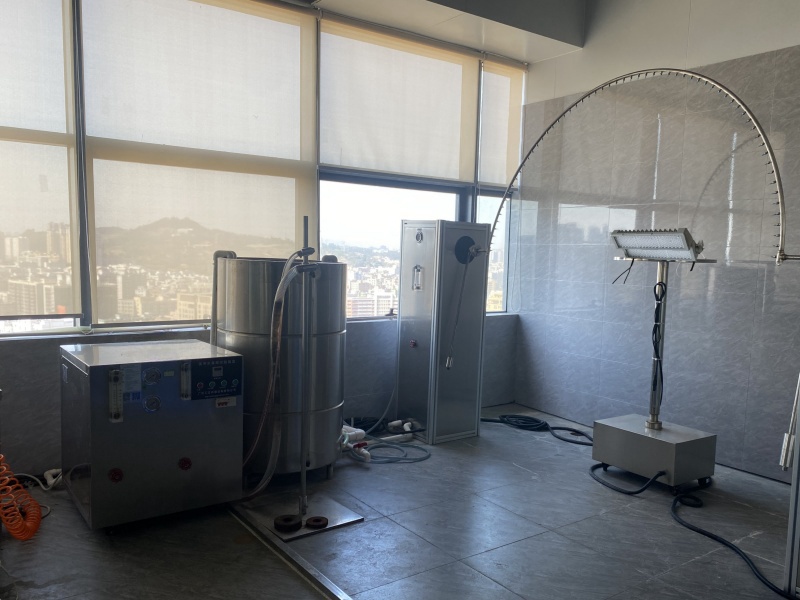
Ingress Protection(IP) Test
Water-proof testing is to ensure that our LED luminaires meet the required level of protection against water ingress, including IPX3 / IPX4 rain-proof test and IPX5 / IPX6 water jet-proof test, as well as IP68 underwater test.
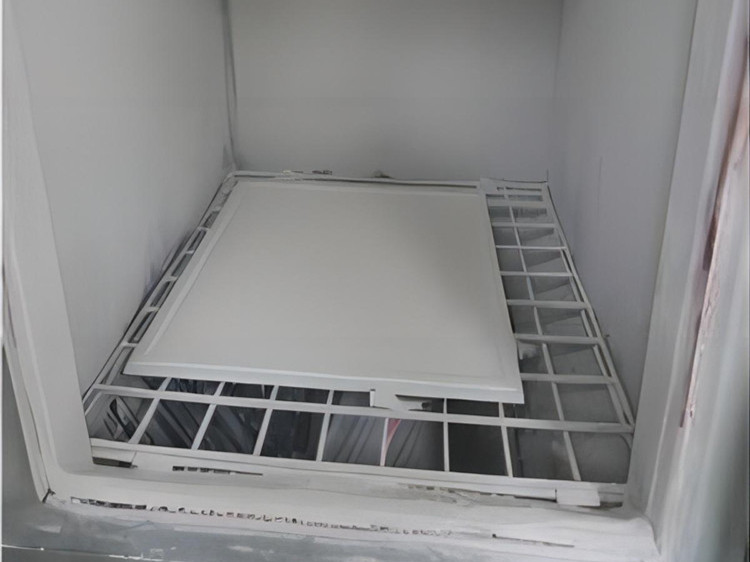
Dust-proof Test
IP5X / IP6X is carried out to identify the level of protection the LED luminaire provides against the ingress of fine dust particles. The luminaire will be opened and inspected to check for dust inside after 3 hours of testing in the dust chamber.
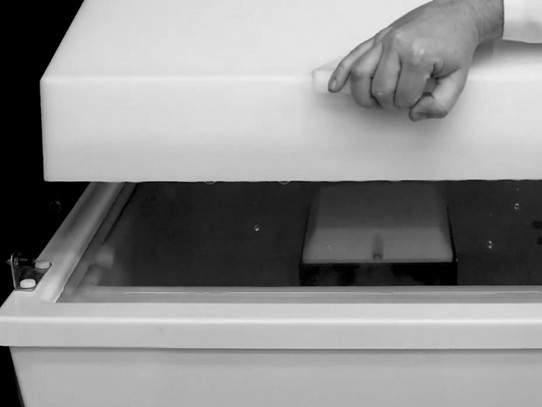
Humidity Test
The relative humidity is maintained between 91% and 95%. Samples are kept in the cabinet for the 48h duration of test.
Check for any damage or deform and then immediately subjected to various of electrical tests.
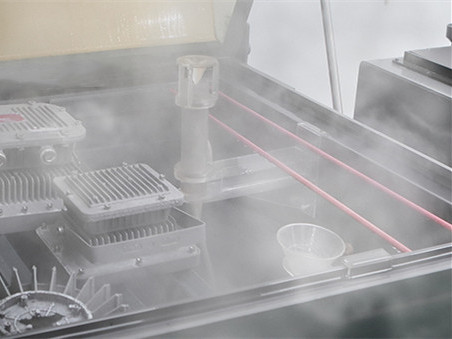
Salt Spary Test
This kind of corrosion-proof testing is to determine the suitability of the coated powder or paint finishes on our LED luminaires. The test samples are inspected after 240, 480, 720 and 1000 hours of exposure.
Blisters, creep, rust, pits and cracks will be looked for when the testing is finished.
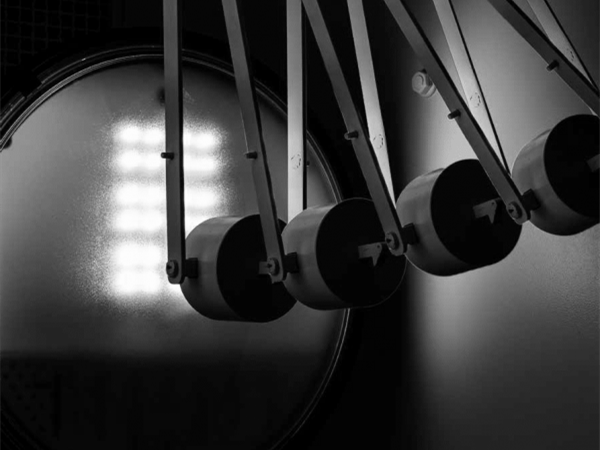
Pendulum Test(- IK10)
The surface of the LED luminaire will be examined before each impact to ensure that there is no damage. Compliance is met if there is no access to live parts.
This pendulum hammer test is up to IK10 and performed 3 times.
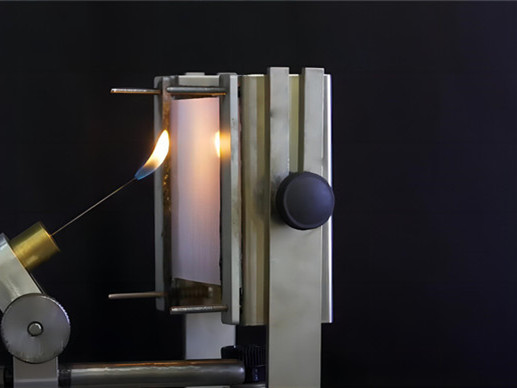
Needle Flame Test
Apply the flame where the highest temperatures are likely to occur for 10s then check results. Needle flame test is to evaluate the resistance to flame of the insulating materials used on LED luminaires.
94V-0 polycarbonate cover on our LED fixtures is of good flame resistance.
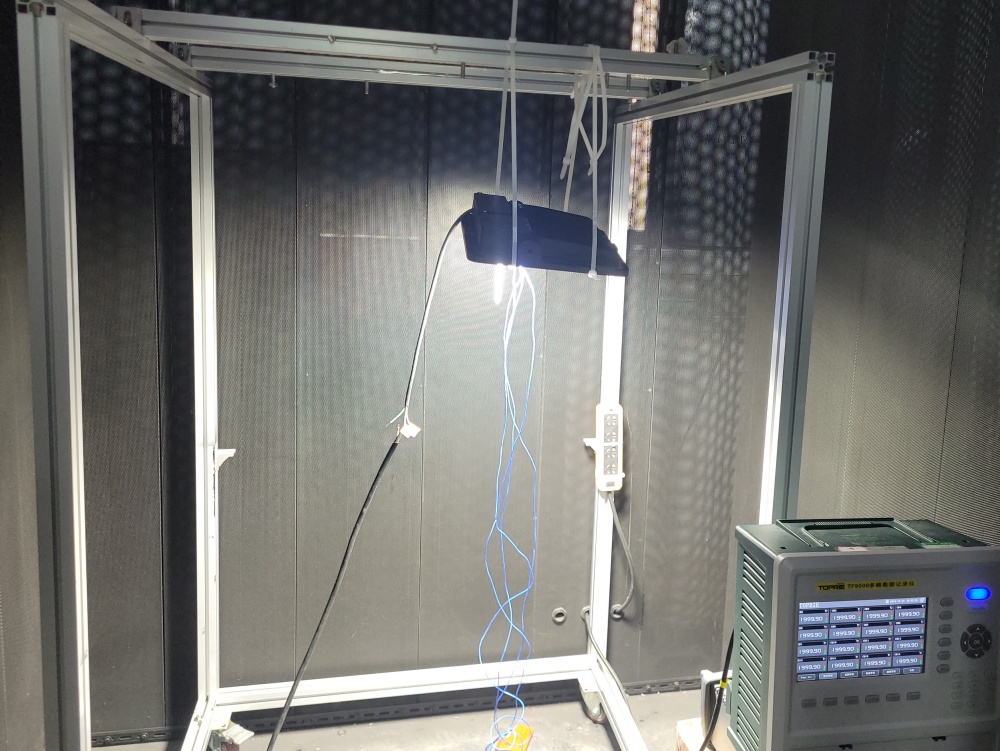
Temperature Rise Test
LED fixture samples are placed in the wind shield to test the temperature rise of the lamp case, driver, PCB and soldering place after 4 hours of continuous operation.
This testing is to verify if the thermal management of the LED fixture is suitable.
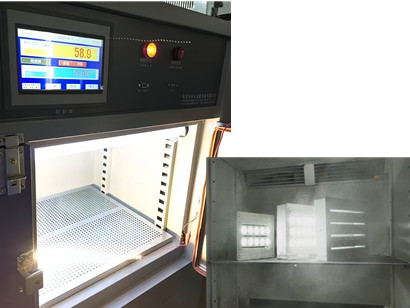
High/Low Temperature Shock Test
Set the cold and thermal shock test chamber low temperature at -40°C and high temperature at 70°C. 20 times of the shock test cycle will be done within 2 hours.
The tested samples should have no obvious damage after testing, and labels should not be cracked, curled or peeled off.
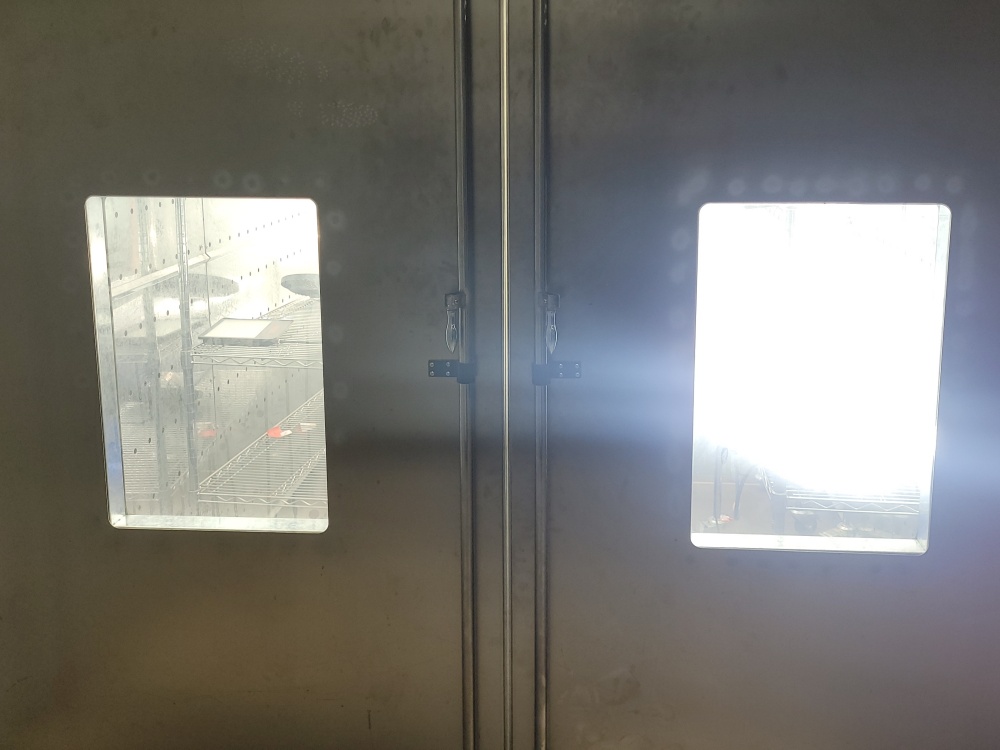
Heat Resistant Test
Temperature of the testing chamber is set at 80ºC to check if the LED fixture can withstand extremely high temperatures, lumen depreciation and driver service time will be recorded.
Combing high-temperature driver and special heat dissipation design, TOPLUMIN has LED fixtures to cope with extremely high temperature applications.
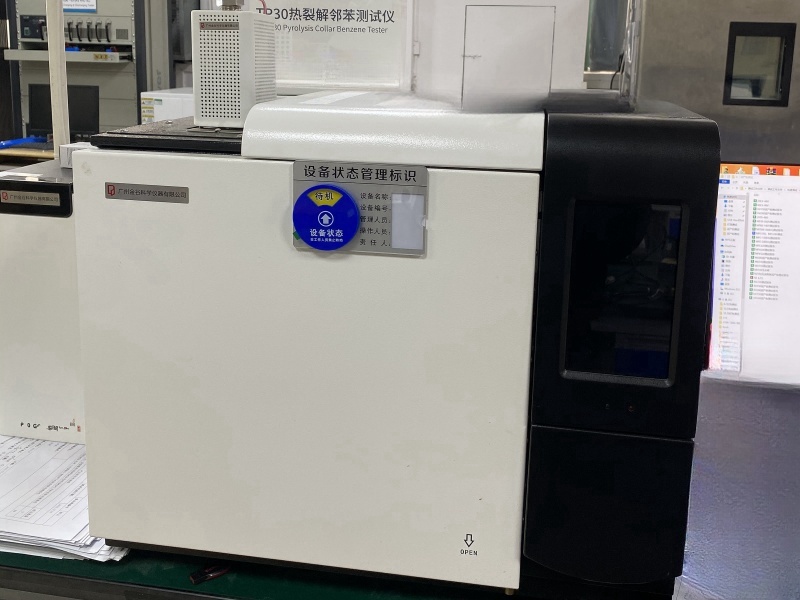
Thermal Cracking O-benzene Testing
Four phthalates were added to the RoHS2.0 restricted substance list on the revised directive (EU) 2015/863 . Specially targeted at rapid screening of the four phthalates to ensure that our LED fixtures comply with the latest ROHS requirements.